Desmond Stephan vises have come up before and almost always with a request for replacement bronze half-nuts. I’d picked up a Desmond some time ago with the intention of making it my main vise and upon cleaning I was having seconds thoughts about the lifespan of the nut.
I was recently cleaning up a Morgan 100 “Rapid Action” and noticed the half nut looked remarkably like my memory of the Desmond. I was actually cleaning the vise to pass on to someone else as it was smaller that my others and was missing the option for a dog. So I dug out the Desmond (which in a mental lapse I’d applied some white lube to) and to my surprise found the half nuts to be the same. The final test was to swap the much fresher Morgan half-nut into the Desmond. The only fiddling I had to do was make sure the half-nut was fully seated and I had to use the spring & pin from the Desmond. The depth of hole for the spring tensioner was different and the softer spring was necessary for smooth action.
I did notice that the thread pitch was a little different between the screws of both vises. I couldn’t take a highly accurate measurements because I don’t have any acme thread gauges. The Morgan screw was ~1.24″ OD and 4 TPI the Desmond screw was ~1.25″ OD and 4.1 or 4.2 TPI, just slightly more than the Morgan. This got me concerned about the TPI of the half-nuts. Given the wear on the Desmond nut it’s a little hard to tell but they both looked the same to my measurement. When I gave some thought to the wear on the Desmond I realized that it was consistent with a slight mismatch in the TPI of the screw and nut.
So, the Morgan 100 and Desmond half-nuts are interchangeable and the high wear rate of the Desmonds might be attributed to some sloppy machining.
The better news is that this part is still available from the owners of Morgan. It’s part 23 “Old Style” nut, item #1141023. I was quoted from a price list $27. Not cheap, but it’ll put a $10 vise back into service. They also have other parts. Contact: sales@milwtool.com
- Morgan nut and spring
- Spring O.D. Inch
- Spring O.D. metric
- Desmond spring and pin length inch
- Desmond spring and pin length metric
- Desmond pin (nail) length inch
- Half nut I.D. inch
- Half-nu I.D. metric
- Morgan spring length inch
- Morgan spring length metric
Above is a gallery of measurements or the spring and pin from the Desmond, and just the spring from the Morgan (I guess the Morgan is supposed to have a pin based on the Milwaukee Tool parts diagram but mine didn’t have one and operates fine). The pin in the Desmond is just a nail that snugly fits the I.D. of the spring. The spring force is similar on both springs, hard to compress by hand.
Hello,
I happen to have a Desmond Stephan w10 that is missing its half nut. After reading your article, I ordered the part from Milwaukee Tool. You also make reference to a spring and a pin, which I must also be missing. Does this engage with the half nut? I can’t see where it would be installed. Thanks in advance for any help. I was very glad to see this article, since I have had this vise for quite a while.
-Andre J. Barbeau
I’ve been meaning to open one of these vises since I posted that. I’ll get some measurements of the pin and spring. You can see the hole they seat into in this image. The part #23 “old style” is pictured in the parts diagram with a spring and pin, which I assumed they’d send with the part (of course we all know what happens when one assumes).
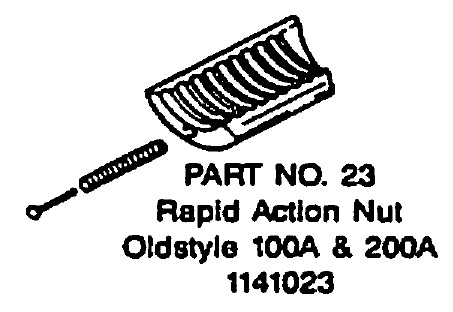
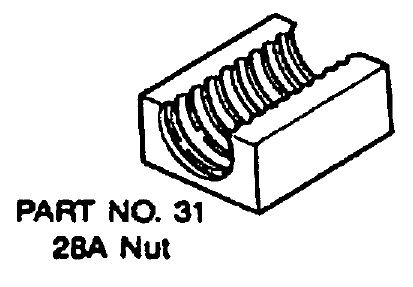
Does your part look like this (correct):
or this (incorrect):
Updated the article with some photos and measurements of the spring and pin for the half-nut.
I have an old Richards Wilcox vise which is missing a brass half screw. (Quick release door). Do you know where I might find one? I want to do a proper restoration.
I’m not sure I have any Wilcox vises to reference. Garage journal or lumber jocks might have information on them.
Hello
I have an old Wilton 4×10 vise and the holf-nut was missing when I bought it.
I can no longer find the parts breakdown picture that lists those parts from milwtool so I gambled and ordered a replacement nut from milwtool. It also seems correct for the wilton but there is a fair gap at the end where the spring/pin comes out. Is there something like a spacer that should go there?
Is there any chance you have a picture of the underside of the cap that holds the half-nut in place? The one that came with the vise has been “modified” and I’m not sure what they did and if it matters
Many thanks
B
I don’t have a picture handy but there is something like a 1/4″ gap on the spring end of the Part No. 23 shown in the above comment photos. I had no idea any of the Wiltons used the same design (my Wilton doesn’t). If the bronze half-nut is snug, it’s fine. If it’s sloppy then I’d get a longer spring + pin combo. If you use another piece as a spacer on either end, then it might slip when the quick-release is operated and jam the screw. It isn’t a precision fit by any means, so as long as the quick-release works reliably then it’s the right fit. Also, remember that the housing that holds the nut in is (probably) keyed to fit one direction and not the other. I was fighting with the Morgan to get the quick-release working until I realized I had assembled it backward.
I have a C.W. Toles #20 vise. The same half nut that works in the Morgan works great for the Toles also. Apparently Toles had the original patent from the paperwork I could find. All I had to do was work the back of the nut down a bit to get it to seat deeper.
I was told my Morgan 200A a later issue model because it has set pins holding in the guide rods…in leu of nuts.
It’s been working fine up until last week when I heard (or actually felt) the jaws “pop” while in the process of tightening on a piece of work.
After that it would clamp down on work (actual holding pressure) only at certain widths of opening…mostly within an 1″ or so from full-close or near its full-open position but not in between.
Now it won’t clamp (with sufficient working pressure) anywhere along its jaw opening. It feels as if it’s tightening to a point then “popping loose”.
I know there is an insert in the bowels of the vise with maybe 60 degrees of machined teeth (the nut) which works against the ACME threaded rod. The nut looks as if it’s made of bronze from what I can tell without completely disassembling the unit… maybe the bronze stripped who knows.
I believe the small spring in the end of the nut (according to exploded views/pictures I have of the vise) is still functioning in some fashion because the vise will still “pop” as mentioned earlier when clamping pressure is applied.
I’ve removed the moving jaw (guide and ACME rods) and peered inside the works. The nut and spring appear to me to be situated where they’re supposed to be. I can remove them if necessary for replacement, though I understand it’s a pain to reassemble if the vise isn’t sitting in my lap. I would need to remove the tabletop… which includes a built-in router station and my table saw to get at the main frame of the vise.
I actually didn’t think that particular portion of the wood vise would/could break under normal use, or I would not have built it so deeply into the table. Here’s hoping that’s not the case.
MY QUESTION:
Do these vises generally exhibit such behavior due only to breakage/strippage or can they become misaligned somehow? I ask this because I would seriously like to “fix” what’s wrong (if possible) without extracting the vise proper from my rolling worktable which would be a somewhat arduous endeavor, though one I’d be willing to undertake if needed.
At this point I’ll stress again the “normal use” part of my oratory…no engine blocks (or similar) were held in the jaws of this vise… not by me in any event;)…bought used off e-bay.
Any help/advise would be greatly appreciated.
P.S.
I removed the nut, spring and nail and all look good…no bends/breaks/cracks or “tooth strippage”. Would the 2 slotted machine screws holding the U-shaped cover to the bottom of the vise cause this behavior?
Thank you very much,
Bruce J
The failure mode you’re describing is exactly what a ‘slip’ failure would be. The fact that when the middle of the screw is engaged it slips, but when either supported end of the screw is engaged it’s OK supports the following diagnosis. There are two main possibilities based on my experience:
1) The nut is moving due to not being seated properly.
2) The nut is actually worn out but looks fine.
3) Something else is wrong.
1) What you are describing is exactly what I had when I reassembled the Morgan (100A). I had tested it months before and new everything was fine, but it kept slipping. It ended being that the cover that holds the nut in was flipped side-for-side and the lip/edge geometry inside that cover was allowing the nut to move (over the ACME screw to flex, I forget now). The cover looked fine from the outside and the two flat-head screw seated all the down but it still made a difference because of the lip inside! That might be the easiest thing to try. I’m not sure I have a photo. If the cover was loose, that could also cause the problem.
2) The nut might be worn out. The screw essentially grinds a brand new thread into the bronze nut over time. It will look shiny, match the screw thread perfectly, and may even be full tooth depth. If the screw can flex a little over the nut, then it will slip. Eventually, with enough wear, the screw will have enough room to move. If you’ve tried both ways with 1) than you might be able to ‘shim’ the nut but putting a few pieces of paper behind the nut. If that works you might want to order another nut.
The fact that you were using it nicely might have covered up the issue. These things aren’t so new and were abused in many environments. Luckily you found the nut cover and didn’t have to take the workbench apart.